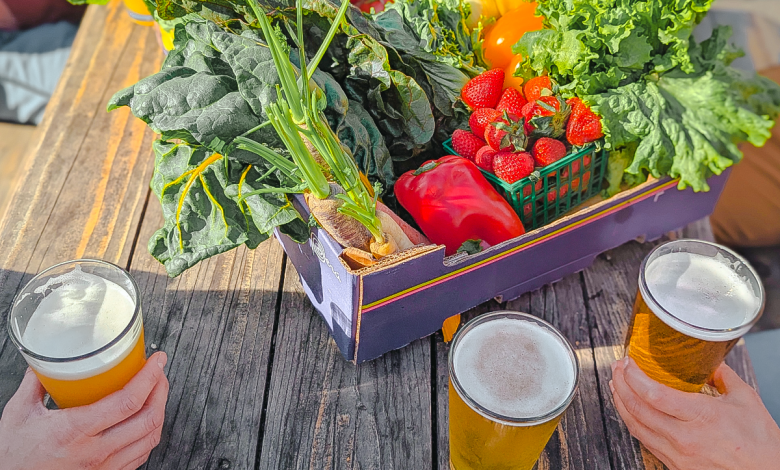
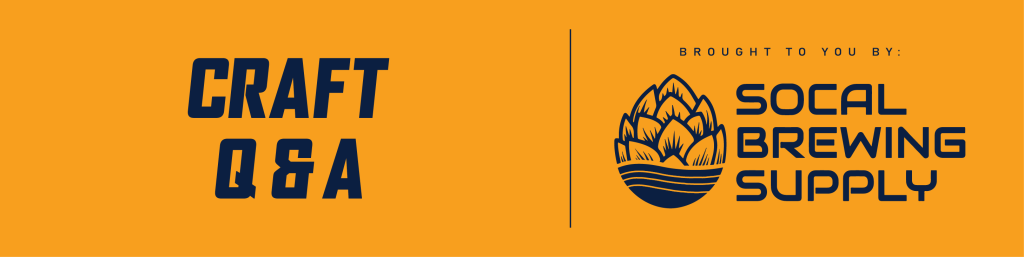
As anyone who’s ever attended an industry conference or even hung out with multiple brewers for after-work shifters can tell you, individuals in this profession have a great deal in common. From the beer styles they prefer to manufacture and consume, to varieties of hops, grain, yeast and the vendors supplying all three, to the passion that not only drew them to the brewing industry but continues to drive them, there is much common ground from one brewery and its fermentationists to another. Over the past decade or so, that has come to include an increasingly common desire to do their jobs in the most environmentally conscious manner possible, reducing waste while making positive contributions to the world around them. In order to do this, many brewing companies form alliances with non-profits and eco-friendly businesses that can guide their internal efforts to produce results felt far beyond their breweries. Having witnessed this form of symbiosis time and time again throughout San Diego County, the head of local business, TerraFerm, is looking to find a brewery he can work with to do just that. The goal is to forge a partnership that allows his company to utilize its patented technology to capture carbon dioxide produced during the fermentation process and funnel it to compartmentalized farms housed within a brewery’s footprint, turning would-be waste into potent fuel. Here, we speak with TerraFerm founder Mathew Halter about the impetus for developing this technology, the benefits it presents, his proposed plan for partnering with local craft-beer companies and what they can get out of doing so.
How did the idea for this technology come about?
In grad school, I worked on lignocellulosic bioethanol feedstock development. We were trying to make ethanol from sources other than corn, and a native grass called switchgrass was proposed as an ideal feedstock crop. So, the Department of Energy spent a lot of money developing all aspects of the ethanol production process, from feedstock growth to feedstock processing and fermentation. I was working on improving cold-temperature photosynthesis to give the crop an extended growing season – earlier in the spring and later in the fall – to help maximize annual yield. In working to optimize photosynthesis, I became very familiar with its underlying mechanisms, and even though switchgrass was always going to be an outdoor-grown field crop, I became well aware of carbon dioxide enrichment strategies used by indoor growers to increase crop yields.
After grad school, I transitioned into the fermentation field. I was hired as a strain and process development microbiologist at a major chemical manufacturer that was using a bacterial platform to produce biopolymers from corn rather than from petroleum. This was a continuous fermentation facility that was producing massive amounts of fermentation byproduct carbon dioxide, which was just being released to the atmosphere. It was during my time there that the idea that is the basis for TerraFerm came to mind. It seemed like a waste to simply be releasing what was, to them, a valueless byproduct, but what could be a valuable input for the indoor farming industry. From there I did some digging on the internet, because I was sure that this must have been done already. When I found that it was not being done, I did some design work and writing that ultimately led to the patent application which was recently accepted. Once the patent was accepted, I was off to the races building a prototype, performing proof-of-concept trials and eventually founding the business to commercialize it.
What did the proof-of-concept process entail?
I wanted to show that this was actually feasible. There were a lot of potential known and unknown issues that needed to be addressed before pursuing a commercial-scale pilot facility with a brewery, so I just wanted to be able to say to brewers and potential investors that this process has been demonstrated. I built a small-scale prototype gas-flow controller that I was able to install on a small-scale fermenter and pipe into a commercial plant-growth chamber. The flow controller wirelessly communicated with a carbon dioxide monitor within the growth chamber and diverted gas flow either to the chamber or to external exhaust, depending on the growth chamber carbon dioxide levels relative to the setpoint. My first test crop was spinach, primarily because it’s a common vertical-farming crop, but also because it’s easy to manage and grow. I grew spinach plants in two growth chambers – a treatment and a control chamber – for 50 days, and brewed a standardized batch of Pilsner beer every four days during that period to maintain a constant source of active fermentative gas production. After 50 days there was a stark difference in growth between the two chambers. After harvest and data analysis, I found that the treatment chamber had produced 89% more spinach than the control chamber, which was an amazing result. A typical yield development program will be looking for single digit returns, so 89 is a big number.
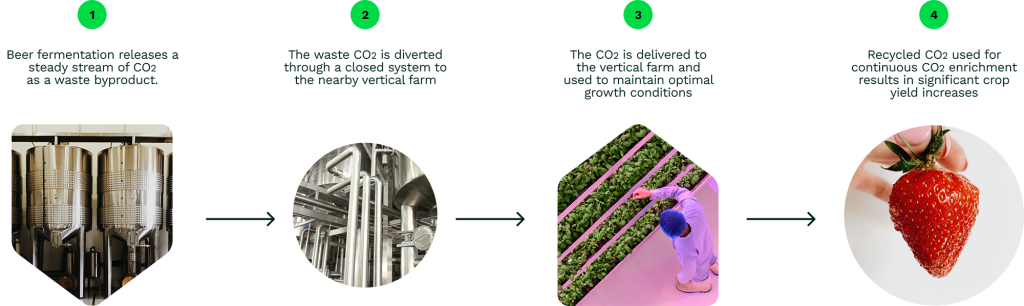
What are the benefits of utilizing this technology?
There are several layers of benefits from both the perspective of the brewer and the grower. The obvious benefit from a business perspective is the yield increase without the overhead required by traditional carbon dioxide enrichment. Right out of the gate, this would allow for a more competitive product to customers that like fresh and locally sourced produce. From the perspective of the brewery, there is also a big marketing opportunity. There are several recent surveys and academic articles that provide strong data showing that beer consumers gravitate to sustainable products. Being able to say to your potential customers that you are doing something meaningful and tangible to decrease your carbon footprint goes a long way. Being able to see and literally taste those efforts while visiting your taproom, I think is a significant value proposition. And last, but certainly not least, is the fact that these partnerships will actually contribute to decreased carbon emissions. Carbon dioxide that would otherwise be emitted to the atmosphere will instead be recycled and fixed in fresh produce. It’s a “use the whole buffalo” strategy that is the basis for the circular bioeconomy that is being proposed to minimize human impacts on the climate and planet. If every industry figures out a way to reuse their waste and byproducts, then each of those small chunks add up to meaningful change. I believe that this is a fantastic opportunity for the vertical farming and brewing industries to partner up to do our part.
What would a brewery partnership look like?
The first assumption people make is that we are looking to partner with a brewery that has a restaurant. That’s definitely not the case. We will market our produce to local restaurants, but we are also hoping to retail our products. The most significant issue we anticipate when identifying partners will be space. In a city like San Diego, free and open space is hard to come by. I would imagine that this would prevent a lot of breweries in the city center from being able to consider us, but there are a lot of breweries in the greater San Diego area, so there are going to be a certain percentage of those that have an open lot out back, a large open space on their brewery floor, a number of unused parking spaces out front or a vacant business space next door. Any of these options would work for us, and we would work with that partner to lease the space where applicable. We are currently in talks with a company called Freight Farms that manufactures off-the-shelf modular shipping container farms, to give an idea of what it would look like. As far as the brewery itself, any and all scales would work, from small to large.
This would really be a symbiotic relationship. TerraFerm would operate the modular vertical farm independently and would not impact brewery operations at all. It would simply involve using our specially designed fermentation locks. They are basically trashcan-style locks widely used in the industry, but are designed to be part of a closed system that would deliver gas flow from the fermentation lock to the vertical farm. This would also eliminate carbon dioxide buildup within the brewery itself, which can be an occupational hazard for brewery staff and customers. We would encourage our partners to sell our products over the counter in the taproom, and we would host a Saturday and Sunday morning farmers market-style booth on site. Our marketing strategy would give the brewery free exposure, and I believe this would be highly beneficial for both parties.
What are long-term goals for TerraFerm?
TerraFerm is an agriculture company at its core. There are a lot of factors currently driving changes in the way we produce our food, from population growth to climate change. I think that access to fresh food is, unfortunately, a privilege that relatively few people enjoy. That needs to change. Providing fresh food to urban centers without the need for massive supply chains that undercut quality is the goal. Our vertical farming capabilities will evolve with the company, and eventually I see us growing along with our early partners to co-develop breweries with permanent, non-modular vertical farms built alongside the brewery infrastructure which are capable of providing millions of pounds of produce per year.